فولاد مارایجینگ گروهی از فولاد های با استحکام فوق بالا و چقرمگی مناسب است که دارای کاربردهای وسیع بوده اما در مقایسه با فولادهای کم آلیاژ عملیات حرارتی شده و سریع سرد شده (کوئنچ) دارای قیمت بسیار بالاتری است. در بررسی های عملیات حرارتی، سرد کردن فولاد های ماریجینگ در هوا و استحاله های فازی رخ داده باعث ایجاد دانه بندی مناسب ریز ساختار همراه با تراکم بالای نابجایی ها میشود. عملیات پیر سختی این گروه از فولاد ها در محدوده دمایی مشخص انجام و در نتیجه دانسیته فاز بین فلزی افزایش یافته که علت آن حضور عناصری از قبیل تیتانیوم، مولیبدن و کبالت میباشد و بنابراین
فولاد ماراجینگ با استحکام بالا از طریق این مکانیزمهای استحکام بخشی حاصل میشود. نام این فولاد از تلفیق دو کلمه مارتنزیت (Martensite) و پیرسختی (Age-hardening) تشکیل شده است.
ترکیب شیمیایی فولاد مارایجینگ و عناصر آن
فولاد مارایجینگ حاوی مقادیر بسیار کمی کربن (حداکثر 0.03 درصد) و مقادیر زیادی نیکل (17 الی 19 درصد) همراه با میزان کمتری کبالت (8 الی 12 درصد)، مولیبدن (3 الی 5 درصد)، تیتانیوم (8/1 الی 2 درصد) و آلومینیوم (1/0 الی 15/0 درصد) است. در فولادهای مارایجینگ به سبب جلوگیری از تشکیل رسوبات کاربید تیتانیوم، میزان کربن پایین نگه داشته میشود و در صورت وجود غلظت بالای کاربید تیتانیوم افت خواص مکانیکی رخ داده و بر اساس آن مقاومت به ضربه و شکل پذیری به شدت کاهش مییابد. همچنین به علت وجود عناصری نظیر کبالت، فولاد مارایجینگ گران قیمت است.
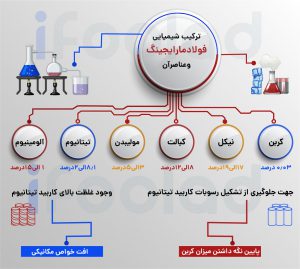
عملیات حرارتی
فولاد مارایجینگ به واسطه حرارتدهی در منطقه آستنیت (در حدود 850 درجه سانتیگراد) تولید میشود که به آن آستینت سازی نیز اطلاق میگردد. از طریق سرد کردن آهسته در هوا یک ریز ساختار مارتنزیتی ایجاد میشود. سرد کردن آهسته فولاد هایپویوتکتیک منجر به تشکیل فریت و پرلیت میشود در حالی که سرد کردن سریع در آب یا روغن منجر به ساختار مارتنزیتی خواهد شد. با این حال به دلیل میزان بالای نیکل در فولاد ماریجینگ میل به جلوگیری از تشکیل فریت و پرلیت زیاد است.
بررسی ریز ساختار فولاد ماراجینگ در مقایسه با فولاد ساده کربنی نشان میدهد که در این گروه از فولادها، ساختار مارتنزیت میزان سختی کمتری را دارا میباشد و بنابراین شکل پذیری و استحکام بالا بدون نیاز به عملیات حرارتی نرم سازی حاصل میشود. پس از سرد کردن، عملیات پیر سختی در محدوده دمایی (480 الی 500 درجه سانتیگراد) انجام تا به واسطه آن توزیع مناسب رسوبات سخت در زمینه مارتنزینی ایجاد شود. از کبالت به عنوان یک عنصر آلیاژی مهم در صنایع استفاده و از آن برای کاهش حد حلالیت مولیبدن و در نتیجه افزایش کسر حجمی رسوبات غنی از مولیبدن استفاده میشود.
به عنوان مثال: Ni3Mo و Fe2Mo. کبالت همچنین به توزیع مناسب رسوبات در زمینه مارتنزینی کمک میکند.
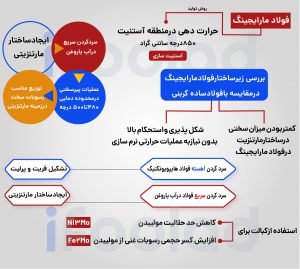
خواص مکانیکی
خواص مکانیکی فولاد مارایجینگ حاوی کبالت و گریدهای استاندارد موجود دارای خواص مکانیکی مختلف بوده که نتایج آن در جدول 1 ذکر شده است. جدول 1: خواص مکانیکی گریدهای مختلف فولاد مارایجینگ به همراه خواص گریدهای مختلف فولاد ماریجینگ

رشد ترک در فولاد مارایجینگ
از مهمترین عیوب ساختاری مشاهده شده ایجاد ترک خستگی و رشد آن بوده که به علت افزایش تراکم نابجایی و شرایط ایجاد شده در مرز دانه این پدیده قابل مشاهده است. همچنین حضور عنصر تیتانیوم در این فولاد تاثیر گذار است و در فولاد مارایجینگ حاوی مقادیر کم تیتانیوم مقاومت در برابر رشد ترک پایین میباشد.
مقاومت به خوردگی
فولاد مارایجینگ در محدوده استحکامی 1240 الی 1720 مگا پاسکال مقاومت خوبی را در آزمایشات انجام شده در آب دریا به نمایش گذاشته است و در بازه زمانی 2 الی 3 سال دچار شکستگی نمیشوند. اگر چه مقاومت به خوردگی کلی خوبی را دارند با این حال بررسی ریز ساختار نشان میدهد که بعد از گذشت 6 ماه ریز ترکها ایجاد و گسترش یافتهاند و بنابراین حفاظت کاتدی امری مهم تلقی میگردد.
ریزساختار فولاد مارایجینگ
بررسی میکروسکوپی نشان میدهد، اندازه رسوبات در زمینه مارتنزیتی میتواند در اندازه نانومتری بوده و همچنین پراکندگی مناسبی در کل زمینه داشته باشند. به علاوه تراکم بالای نابجاییها و نیز تعامل با مرزهای دانه در شکل 1 قابل مشاهده است:
شکل 1: تصاویر میکروسکوپ الکترونی عبوری زمینه روشن از فولاد مارایجینگ
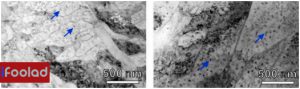
اثر هیدروژن
نسل جدید فولادهای مارایجینگ توسط صنایع هوانوردی توسعه یافتهاند و به لطف کنترل رشد کاربید و رسوبات موجود و عملیات حرارتی پیرسختی از بالاترین استانداردهای مکانیکی برخوردار است. با این حال پژوهشهای انجام شده از اثر مخرب هیدروژن بر روی فازهای رسوب یافته زمینه و افزایش شکنندگی این فولاد حکایت دارد و بنابراین توجه به حلالیت هیدروژن و کنترل کیفیت در صنایع فولاد سازی دارای اهمیت بالایی است.
کاربرد های فولاد مارایجینگ
این گروه از فولاد به جهت خواص خود در صنایع هوا و فضا دارای کاربرد های زیادی بوده که از جمله این میتوان به موارد ذیل اشاره نمود:
• تولید هواپیما • قسمتهای زیرین بالگرد • موتورهای موشک • سایر محصولات نیازمند استحکام بالا
فولاد مارایجینگ به واسطه ترکیب خود استحکام کششی بالا به همراه مقاومت به شکستگی بالا را داشته باشد و این در صورتی است که اکثر فولادها نمیتوانند این دو پارامتر مهم را همزمان داشته باشند. فولاد ماراجینگ به علت خواص ویژه خود دارای کاربرد حیاتی در تولید هواپیما است تا ایمنی مطلوب را حاصل کند.
پیشرفت های نوین
در حال حاضر فناوری ساخت افزودنی و ذوب لیزی انتخابی یکی از پر شتاب ترین فناوریهای عصر موجود است که در تولید فولاد مارایجینگ نیز مورد تحقیق پژوهشگران قرار دارد. استفاده از این روشهای نوین فرصتهای جدیدی را در اختیار مهندسان، طراحان و دانشمندان میگذارد. امکان تولید سه بعدی و تعداد مراحل کمتر تولید باعت میشود این روش در آینده بسیار مهم تلقی گردد.
تولید با استفاده از مواد بازیافت شده
آخرین نتایج تولید فولاد مارایجینگ در حوزه متالورژی پودر با استفاده از پودر بازیافتی نشان میدهد که خواص مکانیکی با تولیدات اولیه یکسان است و در نتیجه استفاده از مواد بازیافتی توجیح پذیر است. بر این اساس در یک پژوهش؛
• استحکام تسلیم: 940 مگاپاسکال • استحکام کشش نهایی: 1127 مگاپاسکال • ازدیاد طول 11 درصدی
گزارش شده است. استفاده از پودر های بازیافتی و تکنیک ذوب لیزری انتخابی یک ایده مناسب اقتصادی برای تولیدات صنعتی محسوب میگردد.