فرایند نورد که یکی از بهترین و کاربردیترین روشهای شکلدادن است، عبارت است از گذراندن بخشی از ماده و تغییر شکل پلاستیک آن از طریق عبور بین غلتکها که در اثر تنش فشاری اعمال شده توسط غلتکها ضخامت ماده کاهش مییابد. دستگاههای نورد در مدلهای دو، سه و چهار غلتکه موجود است. بسیاری از محصولات پرکاربرد ساختمانی مثل تیرآهن و نبشی با مقاطع مختلف به وسیله این فرایند تولید میشوند.
نورد بهتر است یا ریخته گری؟
نورد معمولا با فرایند آهنگری در رقابت بوده و این که کدام بهتر است، به فناوری به کار رفته در آنها بستگی دارد، ولی بهطور کلی از نظر حجم و کمیت تولیدات، فرایند نورد در مقام اول فرایندهای شکلدادن فلزات قرار دارد. هدف مهندسی نورد فلزات عبارت است از تغییر فرم شمش یا ورق به شکل مورد نظر. معمولاً محصول نهایی نورد، تولید ورق یا میلگرد است. پس از اتمام تغییر فرم، محصول نهایی توسط دستگاههای برشی به طول مورد نظر برش داده شده و پس از عملیات تکمیلی و کنترل، بستهبندی شده و به انبار محصول حمل میشود.
از دستگاههای نورد برای گرمکاری و سردکاری فلزات و آلیاژها، در مقیاس های متفاوتی استفاده میشود. برخی از شمشهایی که به تولید ورق فولادی اختصاص داده شدهاند ممکن است ۲۰ تن یا بیشتر باشند و حداقلm 3/0 ضخامت داشته باشند. آلومینیوم را میتوان به صورت نوار ورقهایی به پهنای 4 میلیمتر نورد کرد و از طرف دیگر، ورقهای بسیار نازک آلومینیومی را میتوان با ضخامتی حدودmm 025/0 تولید نمود.
نورد سرد و نورد گرم چیست؟
بسیاری از انواع پروفیل های فولادی محصول دوفرآیند نورد سرد و گرم هستند. نورد از حیث دمای عملیات به دو گروه نورد سرد و نورد گرم تقسیم میگردد. اگر دمای فلز بیش از دمای تبلور مجدد آن باشد، این فرآیند به عنوان نوردگرم شناخته میشود اما اگر دمای فلز زیر دمای تبلورمجدد آن باشد ، این فرآیند به عنوان نورد سرد شناخته میشود. از نظر کاربرد ، فرآیند نورد گرم بیش از هر فرآیند تولیدی دیگر، فرآیند تولید را انجام می دهد و نورد سرد بیشترین تناژ (فرآیند تولید) را در بین تمام فرایندهای کار سرد انجام می دهد.
در رولهای نگهدارنده، جفت رولها با هم در آسیابهای نورد قرار میگیرند که می توانند به سرعت، فلزاتی مانند فولاد را به مقاطع فولادی مثل تیرها، نبشی ها،ریل ها و ... تبدیل کنند. بیشتر کارخانه های تولید فولاد، دارای آسیاب های نورد هستند که محصولات ریخته گری نیمه تمام را به محصولات نهایی تبدیل می کنند.
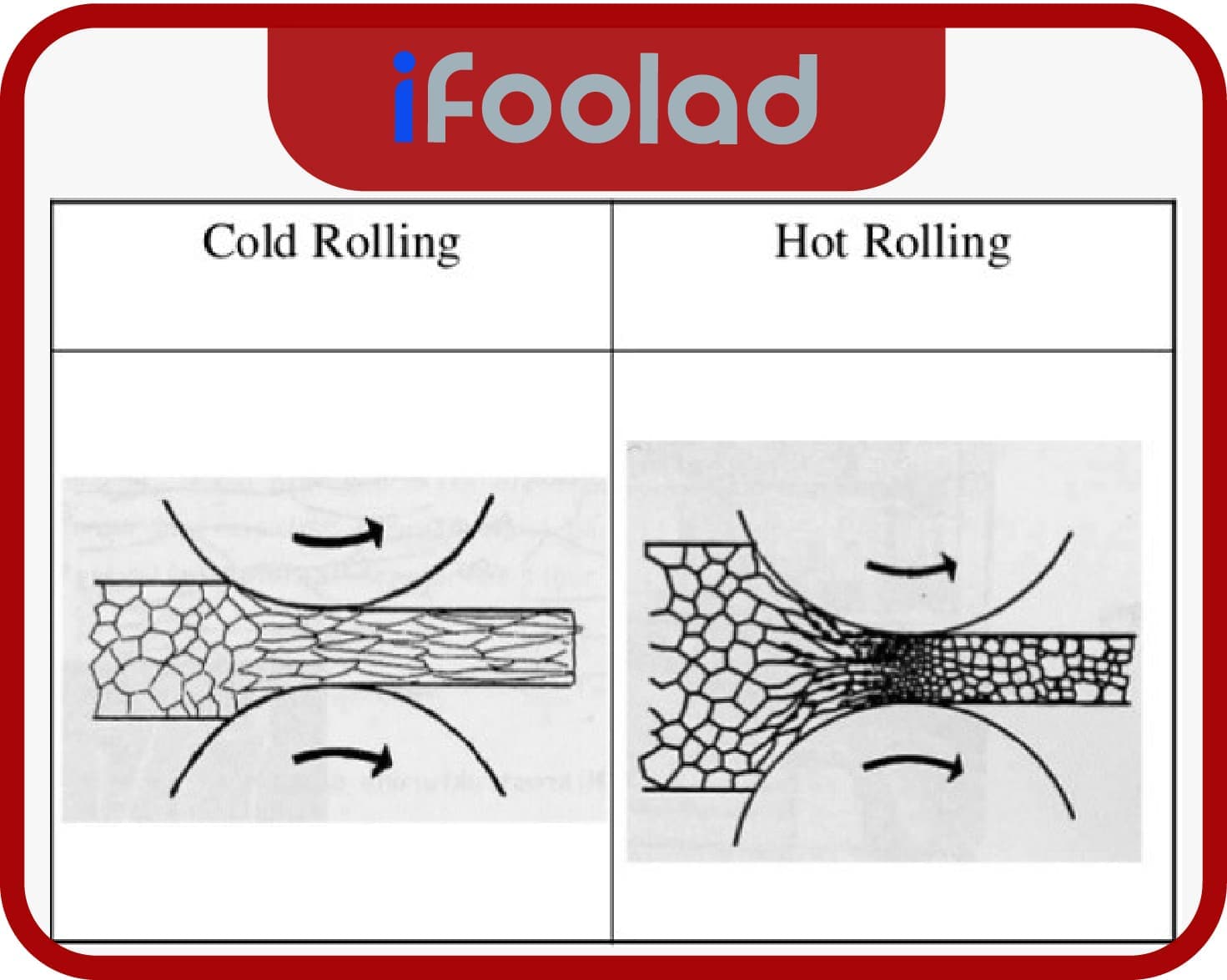
تاریخچه فرآیند نورد
قرن هفدهم میلادی، قرن ظهور روش نورد در صنعت متالورژی بود. در نمونه های اولیه، دو غلتک چدنی در یک چهار چوب چوبی قرار داده میشد و با عبور قلع و سرب از بینشان و کاهش سطح مقطع آنها عملیات نورد صورت میگرفت. به مرور از غلتکهای بزرگتری استفاده شد که نیروی آن به وسیله حرکت اسب و یا توربین های آبی تامین میشد.
استفاده از شیار برای شکل دادن به محصول نورد شده نیز مربوط به این دوران است. سپس برای کاهش نیروی لازم جهت چرخاندن غلتک ها، به جای غلتک های بزرگ از غلتک های کوچکتری که با غلتک بزرگتری چرخانده می شود استفاده شد و به این ترتیب قفسه های چهار غلتکه به وجود آمدند .
با اختراع ماشین بخار محدودیت نیرو برداشته شد و قفسه های نورد بزرگتر شده واز ماشین های بخار قوی جهت نورد شمش ها استفاده شد .با پیشرفته تر شدن و صنعتی شدن صنعت نورد، این صنعت به عنوان جایگزین برای دیگر روشهای شکل دادن فلزها در آهنگری و ریختهگری گردید.
پس از آن و با بهبود فرآیند نورد، دیگر قسمت های کارخانه های شکل دهی فلزات هم پیشرفت کردند. برای مثال، کوره های ذوب ماشین های ریخته گری برای آماده سازی شمشهای اولیه ، کوره های پیش گرم برای گرم کردن شمشها ، خطوط جابجایی، حمامهای اسیدشویی، کوره های عملیات حرارتی، حمامهای آبکاری ماشینهای بسته بندی و … هم بهبود پیدا کردند.
فرآیند نورد گرم چیست؟
همان طور که در بخش قبل ذکر شد در صورتی که دمای فلز بیش از دمای تبلور مجدد آن باشد، این فرآیند به عنوان نوردگرم شناخته میشود.
در نورد گرم فلز از بین دو غلتک که فاصله ی بین آنها اندکی کمتر از ضخامت فلز ورودی و خلاف جهت یکدیگر چرخانده می شوند عبور داده می شود.به دلیل بیشتر بودن سرعت چرخش غلتک ها از ریلی که فلز روی آن قرار دارد، اصطکاک بین غلتک و فلز موجب به جلو راندن فلز شده و طول آن را افزایش و ضخامت آن را کاهش می دهد.
میزان اصطکاک بین غلتک و سطح فلز، معیار کم شدن ضخامت است. به صورتی که برای تغییر شکل زیاد غلتک ها به جای حرکت ماده روی آن می لغزند. در نورد گرم توانایی تغییر شکل بسیار زیاد است. از آنجا که در اثر تبلور مجدد، استحکام تسلیم بهطور قابل توجهی کاهش مییابد، به همین دلیل نیروی لازم برای فرایند نورد قطعات بزرگ در فرایند نورد گرم افت قابل ملاحظه ای دارد.
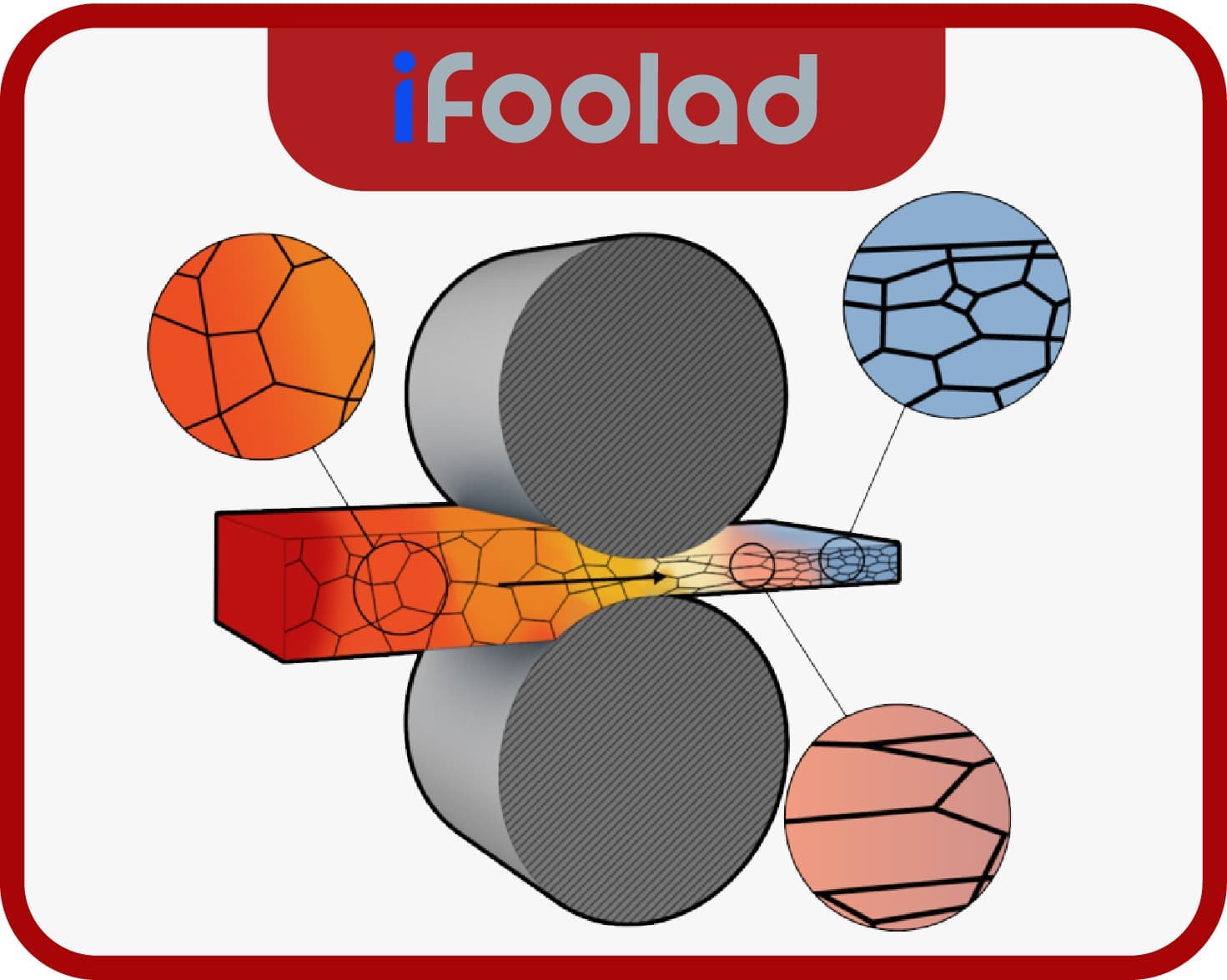
فرآیند نورد سرد چیست؟
با نورد سرد، ورق ها و تسمه هایی میتوان تولید کرد که پرداخت سطحی شده، در ابعاد آنها دقت زیادی به عمل آمده و مقاومتشان افزایش یافته است. این ورقها با ضخامت کم تولید میشوند و پس از طی کارهایی از قبیل اسیدشویی، ضخامتشان کاهش مییابد. به طور کلی میتوان عنوان کرد که عملیات نورد سرد، ورق های فولادی با حذف نقطه تسلی و دقت ابعادی بالا و کیفیت سطحی مناسب تولید می کند.
این نوع نورد که معمولاً در دمای اتاق و حداکثر تا ۲۰۰ درجه سانتیگراد انجام میشود؛ باعث افزایش سختی ماده موردنظر شده و افزایش نابجایی در ساختار کریستالی و افزایش تنش تسلیم را نتیجه میدهد. دراین نوع نورد همان طور که بیان شد محصول در قالب های دمای پایین قرار میگیرد، جایی که قطعه پس از نورد آنیلی یا بازپخت تا دمای اتاق سرد میشود.
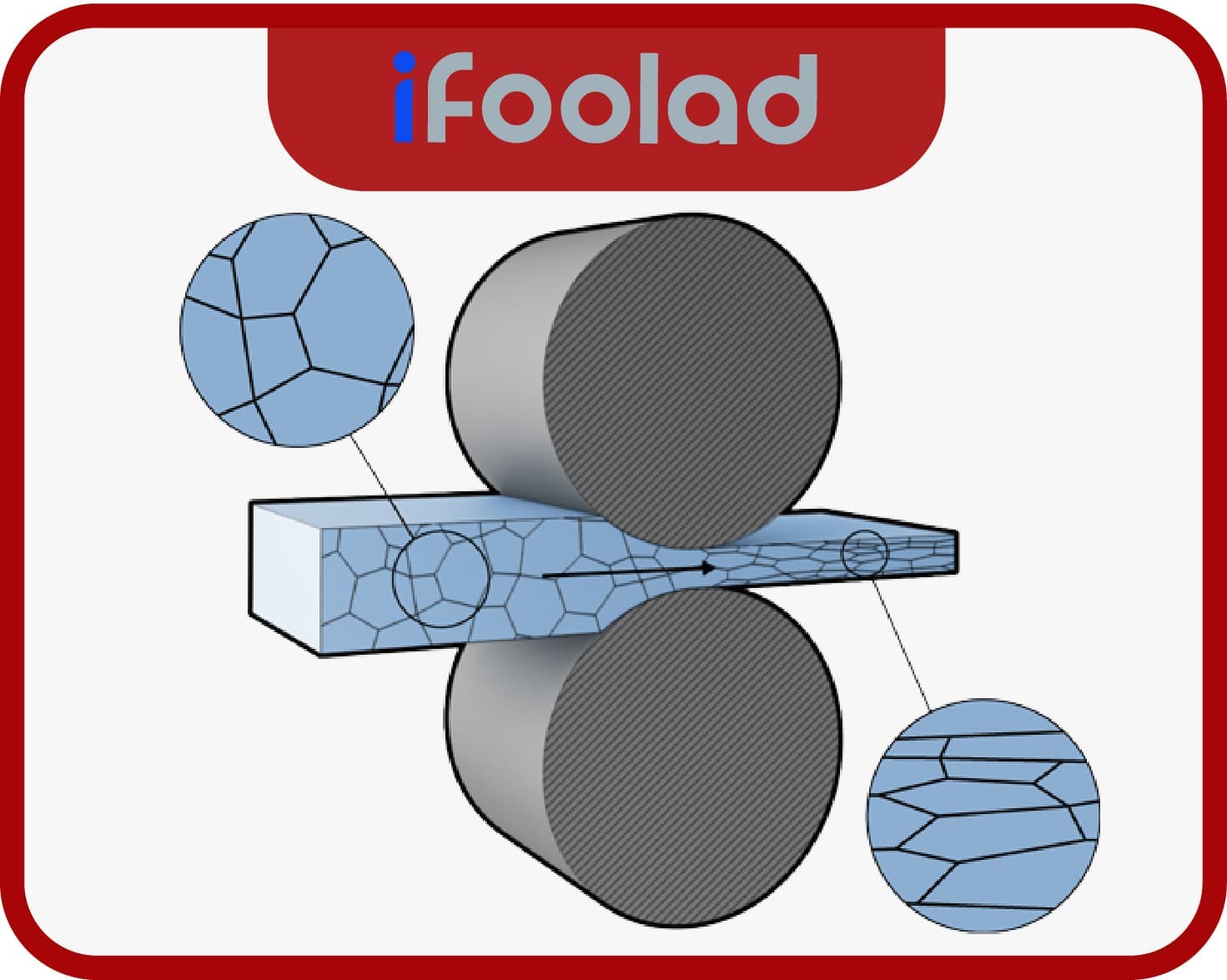
پس از آنیل یک فرآیند نورد پوستهای وجود دارد که در این فرآیند ورقها از لحاظ ویژگیهای مکانیکی و کیفیت ظاهر سطح و موج بررسی شده و عیوب آن برطرف میشود. و در نهایت فولاد با تلورانس ابعادی خوب و محدوده سطح بیشتری تولید میگردد. باید ذکر شود که نوردهای سرد و گرم تنها از نظر نوع ماشین کاری تفاوت دارند و هر دو وظیفه کاهش ضخامت ورق ها و فرمدهی آن را دارند. از این رو نمیتوانیم این دو روش را از هم مجزا بدانیم و در واقع نورد سرد را باید ادامه روش گرم نورد دانست.
برای اطلاع بیشتر درباره شکل دهی فلزات میتوانید به مقالات خمکاری چیست ؟ و چه روش هایی دارد؟ و انواع روش های برشکاری فولاد و فلزات مراجعه کنید.نورد سرد دارای مزیتهای قابل توجهی است که از آن دسته میتوان به موارد زیر اشاره کرد:
- در غیاب سرما و اکسیداسیون، تلورانس کمتر و پرداخت سطح بهتری حاصل میشود. برخلاف نورد گرم که دارای پوشش اکسیدی است.
- روغن کاری سادهتر
- قابلیت تولید ورق با ضخامت کمتر
همچنین از کاربرد محصولات نورد سرد میتوان به محصولات زیر اشاره کرد:
- صنعت خودرو سازی
- تجهیزات ساختمانی
- لوازم خانگی مانند: یخچال، ماشین لباسشویی، ماشین ظرف شویی و ...
- دستگاه های الکتریکی مخازن
مقایسه محصولات نورد گرم و نورد سرد
به طور کل فولاد های نورد گرم دارای کیفیت کمتری نسبت به فولاد های نورد سرد هستند. به این دلیل که بدون سپری کردن زمان و یا فرآیند خاصی به صورت مستقیم در پروسه تولید قرار می گیرند بنابراین به گرمایش مجدد فولاد نیازی نیست. هنگامی که دمای فولاد کاهش پیدا می کند، حجم آن نیز کم میشود بنابراین میزان کنترل برای تغییر سایز و شکل فولاد در دمای بالا در مقایسه با نورد سرد کمتر است.
از ورق گرم برای تولید محصولاتی با مقیاس بزرگ استفاده می شود. معمولا ورق گرم در مواردی استفاده می شود که کیفیت ظاهری اهمیتی نداشته و خواص مکانیکی کالا اهمیت داشته باشد. فرآیند نورد گرم مزایا و معایب مختلفی دارد که از جمله آنها میتوان به موارد زیر اشاره کرد:
- به نیروی کمتری در طی فرآیند نسبت به نورد سرد احتیاج دارد.
- تجهیزات و دستگاههای کمتری برای نورد گرم استفاده میشود.
- کرنش سختی کمتری در طی فرایند روی قطعه انجام میشود .
- قطعه ی فلزی تولید شده دارای استحکام کمتری نسبت به محصولات تولید شده توسط نورد سرد است.
- نورد گرم برای شمش های بزرگ مناسب است.